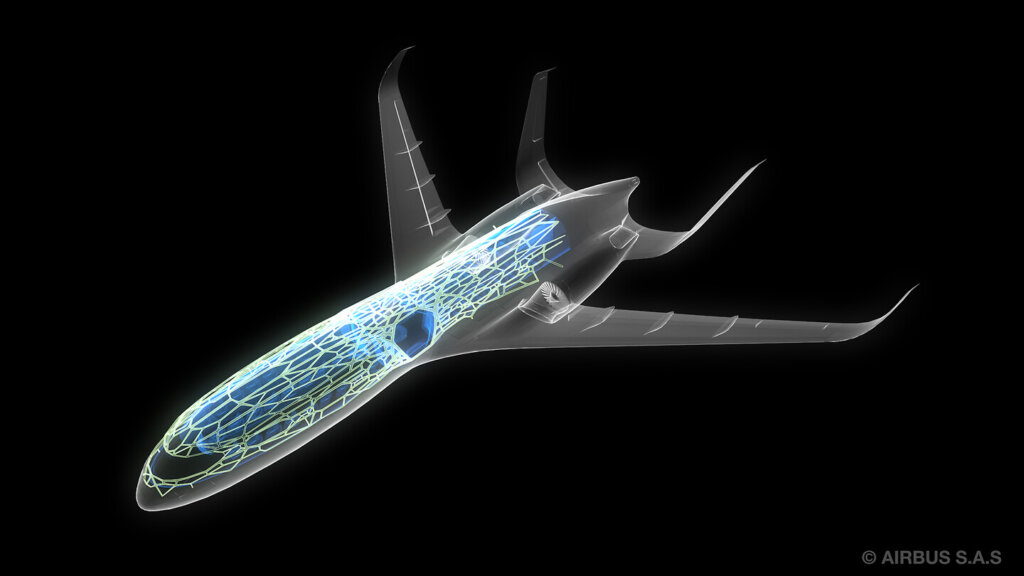
It’s been a consultant for NASA, shot at by police and mistaken for an alien. How slime mold–a brainless, single-celled organism–mapped the dark universe, keeps challenging the top minds to rethink what intelligence even is and has an ability to fill us with wonder beyond the human kind.
No one would guess human bones and slime mold would lead a design trend. Definitely not a billion dollar one. But the epically odd duo earned seats at the design table, and the results make you wonder why every design team doesn’t consult them from the start.
Effective innovations to slash aerospace emissions is a topic constantly flying around sustainability discussions. With the hottest days ever (note: this has been updated to the hottest year) marking 2023 and double the number of commercial aircrafts in service predicted by 2042 (up to 48,600), we need bold solutions beyond electric air taxis and greener fuels. Now, with the help of an impressive motley crew—slime mold, human bones, generative design, improved materials and 3D printing—an unexpected solution for a better aircraft not only exists, it’s out of the lab and in the skies.
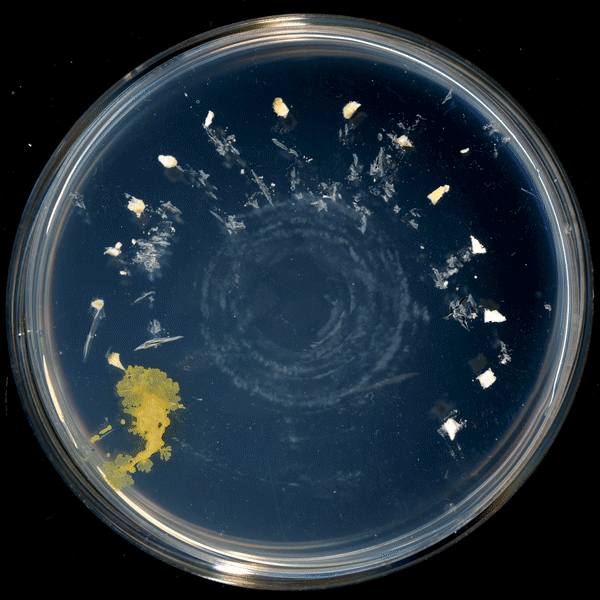
The reason experts are turning to slime mold and bone is a convincing one: nature-based algorithms are capable of designs that traditional approaches can’t come close to. Slime mold’s algorithm gets rid of unnecessary material while bones remove heft where strength isn’t necessary. Not only that, but when coupled with generative design, AI and 3D printing, the entire design and production processes radically transform. While the field of generative AI is nascent and the implications are still unfolding, it is clear that with bio-inspired generative design, what was ten design options becomes tens of thousands of design options; what was a singular human idea becomes a co-collaboration backed by a proven pro with hundreds of millions of years of experience.
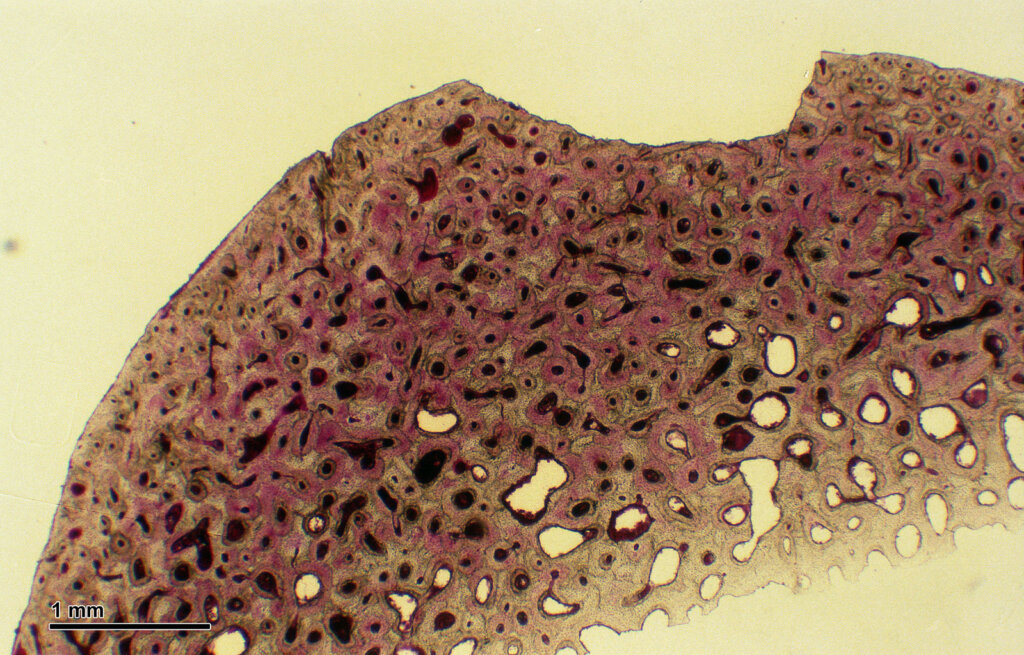
To explore the potential of this technology in aerospace, a collaboration involving Airbus, Autodesk, The Living, Autodesk Studio and APWorks brought slime mold and human bones into the mix. They started with the cabin partition. If this overlooked, but key part of the plane proved to be a strong proof of concept demonstrating a high-performance, lighter (think carbon reduction, fuel savings) design, it could be scaled to other parts of the aircraft. The final design is now known as the Bionic Partition. The results:
- A cabin partition 45% lighter than traditional Airbus designs – 143 lb to 66 lb.
- 3D printing resulted in 95% less raw material saving money, material and emissions
- As weight was slashed, efficiency skyrocketed – for every 2.2 lbs reduction in weight the jet fuel use is cut by 232.2 lbs (~ 35 gallons)
- The Bionic Partition is now the world’s largest metal 3D printed airplane cabin component.
This 23-second clip shows what bio-inspired regenerative design looks like, and why some think of it as the survival of the fittest evolutionary process on steroids. Here, designers input key goals and constraints around the project and the system computes thousands of potential solutions based on algorithms modeling the logic of slime mold and bone. Credit: The Living
Bio-inspired regenerative design is like survival of the fittest on steroids, where innovations are driven by a 3.8 billion-year-old R&D lab converging with AI and human ingenuity.
In case you aren’t as familiar (like me!), generative design is an iterative, exploratory design process where new content is created based on existing data. Designers and engineers use software technology that takes key goals and design constraints around a project into consideration, and generates design results that can be adjusted and evolved based on feedback.
In bio-inspired generative design, the design and production solutions are anchored in nature’s sophisticated algorithms and systems. Think of the process as survival of the fittest on steroids. Innovations are fueled by an R&D lab that’s 3.8 billion years old converging with human ingenuity and AI. When embodying biomimicry’s ethos element, the species’ survival tricks aren’t limited to the organism. We all benefit. Especially when innovations, like this one, have a path towards minimizing negative impacts on Earth at the scale major industries like aerospace can.
When creating the Bionic Partition, designers input algorithms modeling the logic of slime mold and bone, as well as key info (design goals, material preferences, spatial requirements, cost limits, air flow). The technology took all of this into consideration and rapidly computed thousands of design optimizations that humans wouldn’t come up with on our own, which were then evaluated and fine-tuned. The tool can quickly adjust to real-time data, testing and tweaking what is successful and what is not without having to produce a thing. The selected design was then printed using additive manufacturing. (For more, AskNature has a fantastic description of bio-inspired generative design software here.)
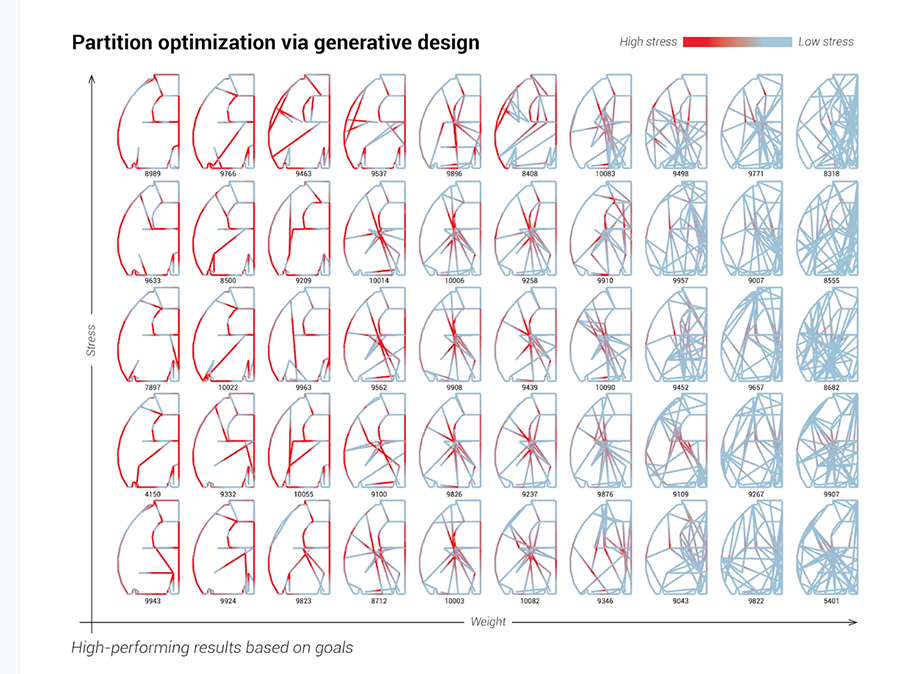
The case for slime mold and bones seems strange till you take a closer look.
Nature’s lab draws the most significant inventors of our time. The cross-disciplinary collaborators were chosen because they are masters of efficiency, redundancy and strength. When translated into an aerospace design, that means less weight, fewer emissions, fuel savings and a high-performance, more sustainable (dare we say wilder!) aircraft.
- Why slime mold? The larger, lacey “macro frame” that makes up the overall structure was designed with the input of the slime mold algorithm because they are masters of efficiency, reinforcing strong connecting points and getting rid of unnecessary material while maintaining strength.
- Why bones? The “micro frame” part of the partition was filled in with grid structures inspired by mammal bones, which are strong at points of stress, but remove heft where strength isn’t necessary. As noted in Biomimicry 3.8, “the internal structure of bone is optimized for strength, but lightweight thanks to a latticework of fibers managing both tensile and compressive forces.”
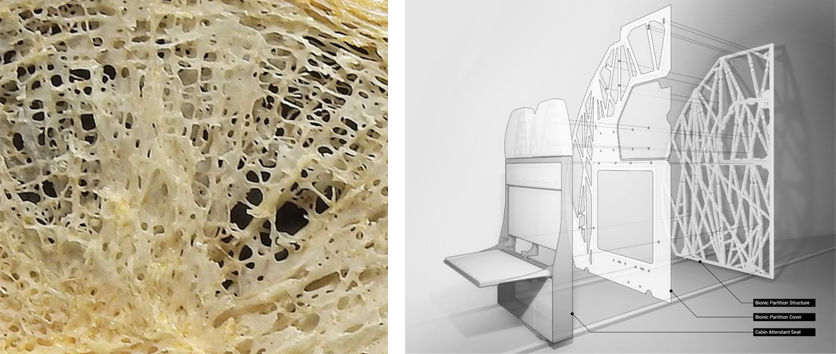
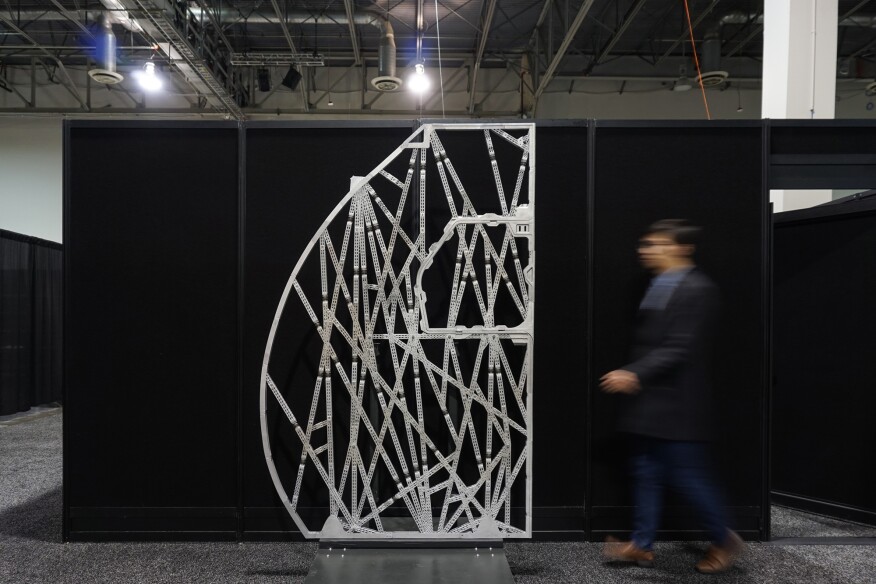
With bio-inspired generative design, the hard line between technology and biology is blurred. In that blur could be one of the biggest breakthroughs in manufacturing.
While the Bionic Partition proof of concept focused on cabin partitioners, this “bio computation” design innovation could be scaled to virtually the entire plane body showing the possibilities in product innovation and helping to decarbonize an industry infamous for emissions. When applied to A320 planes on backorder, the Bionic Partition could save up to 1 million metric tons of carbon emissions per year. According to Mongabay, emissions from global aviation are around 1 billion tons of CO2 per year — more than the emissions of most countries. That number is still going up.
If a single, ancient cell and a human bone can get us all closer to a future we want, and we’re willing to pay attention (and apply!) their guidance, we’re on our way somewhere we want to be.
This is the Part 4 of our 8-edition blog series on slime mold by guest writer Katie Losey. She answers your top questions on this fascinating organism and dives into how a brainless, single cell is capable of shaping our futures and blowing our minds. Read part 5, “Beyond EV and AI: Is Slime Mold Driving the Future of Car Innovation?” here.
Main image credit: Airbus S.A.S
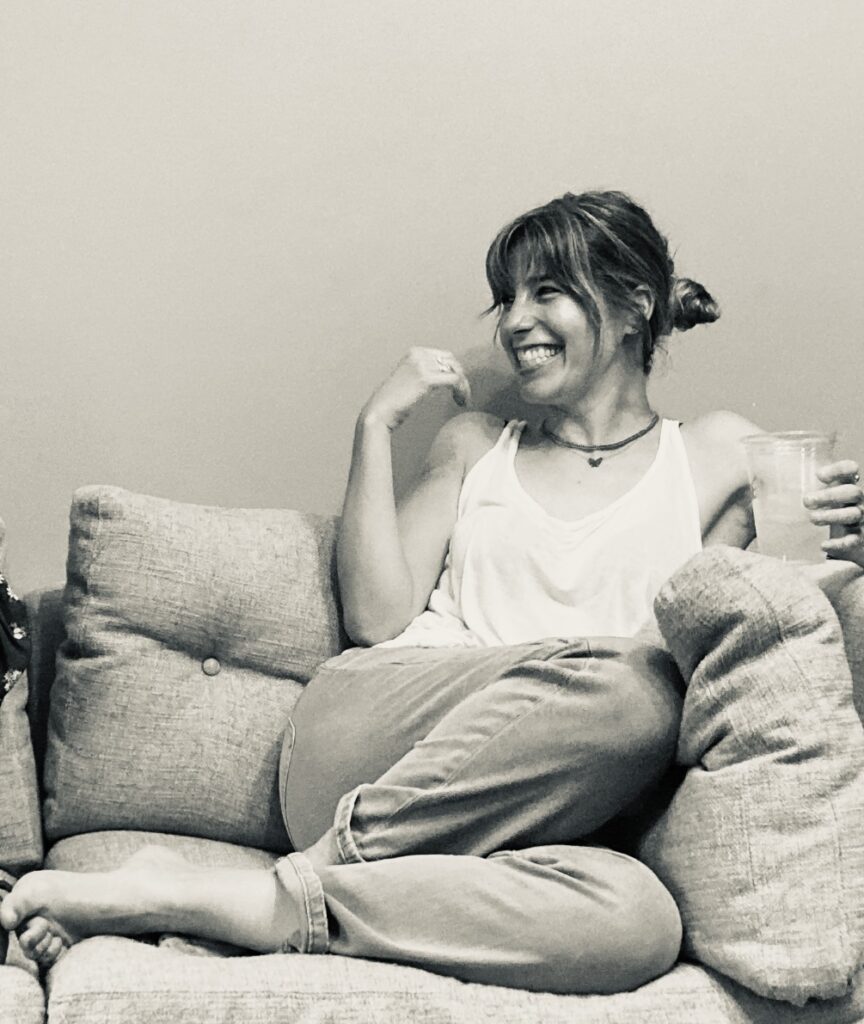
About the author
Katie Losey is committed to bridging the gap between humans, nature’s genius, breakthrough innovations and overlooked wonder. She has worked at the intersection of business and conservation for two decades. In her work she has taken on many roles, including marketing director, writer, and strategist for companies in travel, conservation, nonprofit, and energy sectors. In these roles, she was further exposed to the possibilities of innovation inspired by nature from locking eyes with gorillas in Rwanda and swimming alongside orcas in Norway to dodging rats in NYC! Katie has been a member of The Explorers Club since 2015 and serves on their Public Lecture, Film and World Oceans Week Committees. She has been guest writing for the Biomimicry Institute since 2019, and her science writing has been featured in courses at the U of Cambridge, Johns Hopkins U, and on the cover story of the U of Richmond Magazine (her alma mater). She lives in NYC. Connect with Katie on Instagram and LinkedIn.